When you’re shopping for an impact wrench, you need to consider a few things. You need to think about what you’re going to use it for, what kind of work you’re going to do with it, and what you like in terms of power source and ergonomics. Here’s a guide to help you make a good decision.
Understand the Types of Impact Wrenches
Impact wrenches can be divided into three categories based on their power source:
- Electric (Corded or Cordless): Electric impact wrenches are the most versatile and come in a wide range of power options. Cordless models offer the most portability but may not be as powerful as corded models.
- Pneumatic (Air-Powered): Air impact wrenches require an air compressor but typically provide the most torque. They’re ideal for automotive and industrial applications.
- Hydraulic: Hydraulic impact wrenches are used for heavy-duty applications and offer a lot of power, but they’re less common for general consumer use.
- For more information please refer to our previous article.
Consider the Size
The “drive square” of an impact wrench is the square-shaped connector at the end of the wrench. This is where you attach sockets to the wrench. The size of the drive square determines the size of socket it can accommodate, and it’s an important thing to consider when you’re choosing an impact wrench for specific tasks. Drive square sizes are usually measured in inches and indicate the compatibility with socket sizes.
Here are the common drive square sizes for impact wrenches:
- 1/4-inch: drive impact wrenches are ideal for small, light-duty tasks that require precision rather than high torque. They’re commonly used in electronics, light automotive work, and small machinery repairs.
- 3/8-inch: drive impact wrenches are a versatile size that strikes a balance between the lightweight 1/4-inch and the more robust 1/2-inch. They’re suitable for general automotive work and larger household tasks.
- 1/2-inch: 1/2-inch drive impact wrenches are the most popular size for professional and heavy-duty applications. They offer a good balance of torque and versatility. They’re widely used in automotive repair, construction, and heavy machinery maintenance.
- 3/4-inch: Less common for general consumer use, this size is geared towards industrial and heavy equipment applications that require high torque.
- 1-inch: Primarily used in industrial settings for very heavy-duty work, such as in construction and heavy machinery maintenance, where maximum torque is needed.
Choosing the right drive square size depends on the work you’re doing, the size of the sockets you want to use, and how much torque you need. Each size has a different purpose, from delicate tasks that require precision to heavy-duty tasks that require a lot of power.
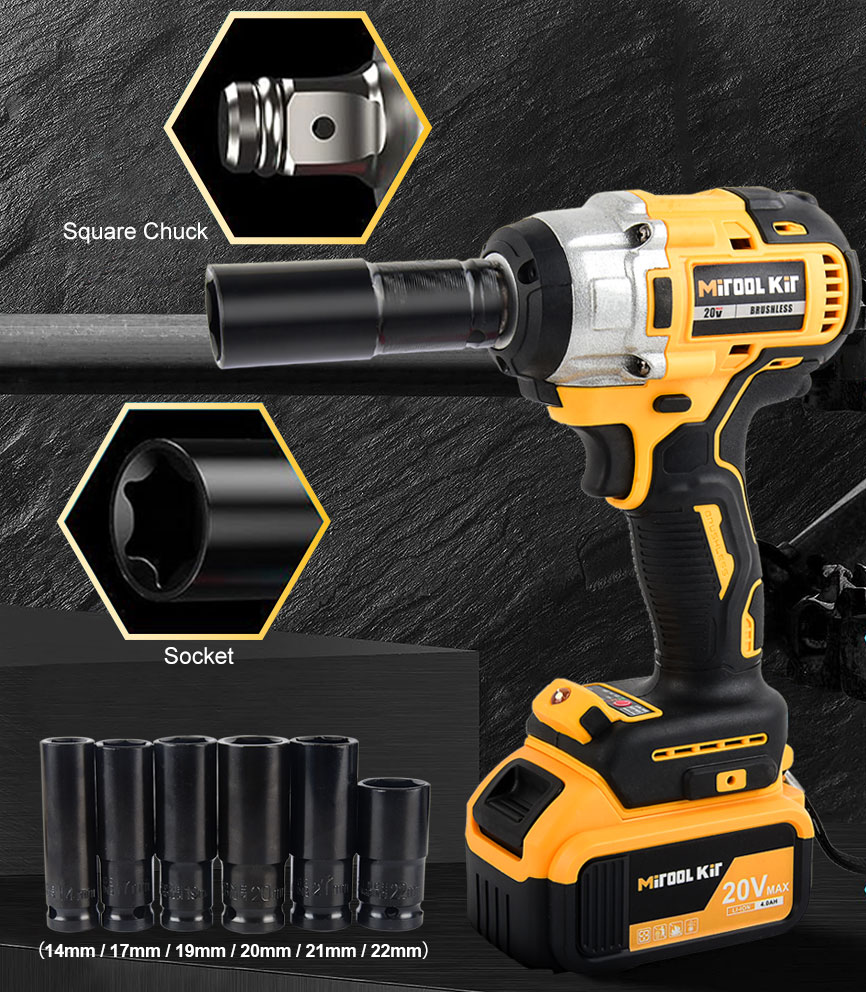
Torque Requirements
When you’re choosing an impact wrench, it’s important to understand the torque requirements for the work you’re going to do so you can choose a tool that can handle the work efficiently. Torque is the rotational force the impact wrench applies and is measured in foot-pounds (ft-lbs) or Newton-meters (Nm). The requirements vary widely depending on the application, from automotive repairs to construction to heavy industrial work. Here’s a comprehensive guide to help you determine the torque needs for various applications:
Automotive Work
- Lug Nuts: Most automotive repairs require between 80 and 150 ft-lbs (108 to 203 Nm) of torque. Larger or commercial vehicles may require more, upwards of 500 ft-lbs (678 Nm).
- Engine Bolts: Torque requirements for construction and home projects can range from as low as 10 ft-lbs (13.5 Nm) for small, delicate components to over 250 ft-lbs (339 Nm) for larger, structural parts.
Construction and Assembly
- Framing and Decking: Fasteners in these applications might need torque settings from 50 to 250 ft-lbs (68 to 339 Nm).
- Heavy Equipment Assembly: Large bolts can require anywhere from 100 to over 1,500 ft-lbs (135 to 2,034 Nm), especially in industrial machinery.
Industrial and Heavy Machinery
- Machinery Maintenance: Bolts and fasteners on industrial machines often require high torque, sometimes exceeding 1,000 ft-lbs (1,356 Nm).
- Structural Steel Fastening: For construction involving steel structures, torque requirements can range from 100 to over 1,000 ft-lbs (135 to 1,356 Nm).
General Use
- Home DIY Projects: Lighter-duty projects typically need between 30 and 150 ft-lbs (40 to 203 Nm) of torque, which is suitable for smaller, handheld impact wrenches.
- Shop and General Maintenance: A mid-range impact wrench with 150 to 250 ft-lbs (203 to 339 Nm) of torque can handle a variety of tasks, from equipment maintenance to disassembling machinery.
Key Considerations
- Over Torquing: Having too much torque can cause damage to materials or fasteners. If precision is critical, choose an impact wrench with adjustable torque settings.
- Under Torquing: If you don’t have enough torque, you won’t be able to tighten fasteners properly. Make sure the impact wrench you choose has a maximum torque rating that exceeds the requirements of your heaviest-duty tasks.
- Type of Impact Wrench: Pneumatic (air-powered) wrenches often offer the highest torque and are common in automotive and industrial applications. Electric (both corded and cordless) wrenches are more portable and sufficient for most tasks.
- Specific Manufacturer Specifications: Always refer to the manufacturer’s torque specifications for critical components, especially in automotive and industrial applications. This is to make sure you’re safe and you’re doing it right.
- Material Considerations: The type of material (e.g., steel, aluminum) can significantly impact the appropriate torque level. Aluminum components generally require less torque than steel components.
- Bolt Size and Grade: Larger and higher-grade bolts will typically require more torque. The grade of a bolt usually indicates its strength and therefore its tightening torque.
- Use of Torque Wrench: For precise applications, using a calibrated torque wrench is essential to make sure you’re doing it right and you’re not over-tightening or under-tightening.
Choosing the right impact wrench is all about balancing the torque needs of your projects with the wrench’s features and capabilities. Think about the toughest tasks you’ll tackle to make sure your wrench has the power it needs. Just remember, models with more torque might be heavier and cost more.
The table below gives a detailed look into the variety of torque requirements across different applications, showing why it’s so important to be specific and stick to professional guidelines. Whether you’re working on a car, building a building, or putting together home furniture, knowing the right torque setting is key for safety, performance, and durability.
Application | Torque Requirements | Torque Requirements | Notes |
---|---|---|---|
(ft-lbs) | (Nm) | ||
Automotive Lug Nuts | 80 to 150 | 108 to 203 | Passenger vehicles; trucks/SUVs may be higher |
Small Engine Bolts | 10 to 20 | 13.5 to 27 | Small engines and machinery |
Large Engine Head Bolts | 50 to 70 | 68 to 95 | For larger engines, varies by manufacturer |
Automotive Suspension Bolts | 100 to 150 | 135 to 203 | Critical for safety, check specific specs |
Construction Framing | 50 to 100 | 68 to 135 | Wood framing, decking screws |
Heavy Structural Bolts | 150 to 1,000+ | 203 to 1,356+ | Steel construction, bridges, buildings |
Machinery Flange Bolts | 150 to 500 | 203 to 678 | Large machinery and equipment assemblies |
High-Torque Industrial Bolts | 500 to 1,500+ | 678 to 2,034+ | Heavy industrial, requires specialized tools |
DIY Furniture Assembly | 18 to 35 | 24 to 47 | Home furniture kits, small structures |
Bicycle Assembly | 5 to 14 | 6.8 to 19 | Critical components like pedals, seat post |
Shop Maintenance | 30 to 250 | 40 to 339 | Wide range for different equipment needs |
Ergonomics and Ease of Use
An impact wrench is a tool made to give high torque output with little effort from the user, making it a must-have tool in various industries, especially car repair, construction, and assembly work. Here’s a quick look at how easy it is to use impact wrenches and how they feel in your hand:
Ergonomics
- Design: Impact wrenches are usually designed with your comfort in mind. Many models have ergonomic handles and grips that fit the shape of your hand, reducing tiredness during long use. Rubberized or soft-grip materials are often used to make them more comfortable and easier to control.
- Weight and Balance: The weight of an impact wrench is a key factor in how comfortable it is to use. Lighter models put less strain on your arm and shoulder, making them easier to use for a long time. The balance of the tool also affects how comfortable it is to hold and use, especially when you’re working in awkward positions or tight spaces.
- Vibration Reduction: High torque and rotation can create a lot of vibration, which can lead to hand-arm vibration syndrome (HAVS) over time. Many impact wrenches include anti-vibration technologies to lower this risk, like vibration dampening handles and mechanisms that spread the torque evenly.
- Noise Level: Impact wrenches can be really loud, potentially causing damage to your hearing. Ergonomic designs often include features that lower noise levels, but even so, it’s a good idea to wear proper hearing protection.
Ease of Use
- Power Source: Impact wrenches can be powered by electricity (corded or battery-powered) or compressed air. Battery-powered models give you more freedom to move around because they don’t need a power outlet, but they might be heavier because of the battery. Pneumatic models are usually lighter and provide steady power but need an air compressor, which limits how much you can move around.
- Torque Adjustment: Modern impact wrenches often have adjustable torque settings, which let you tailor the output to specific tasks. This reduces the risk of overtightening or damaging materials.
- Speed Control: Variable speed triggers are a common feature that gives you control over the tool’s speed, making it more precise and adaptable to different tasks.
- Quick Socket Changes: To make you more productive, many impact wrenches come with easy-to-use socket retention systems. This lets you quickly and easily change sockets without needing any extra tools.
Overall, comfort and ease of use are key, especially for professionals who use these tools for a long time. A well-designed impact wrench should be ergonomic, balancing weight and power to minimize tiredness. Our engineering team at Autojare focuses on creating tools that are not just powerful but also comfortable to use, showing our commitment to quality and user satisfaction.
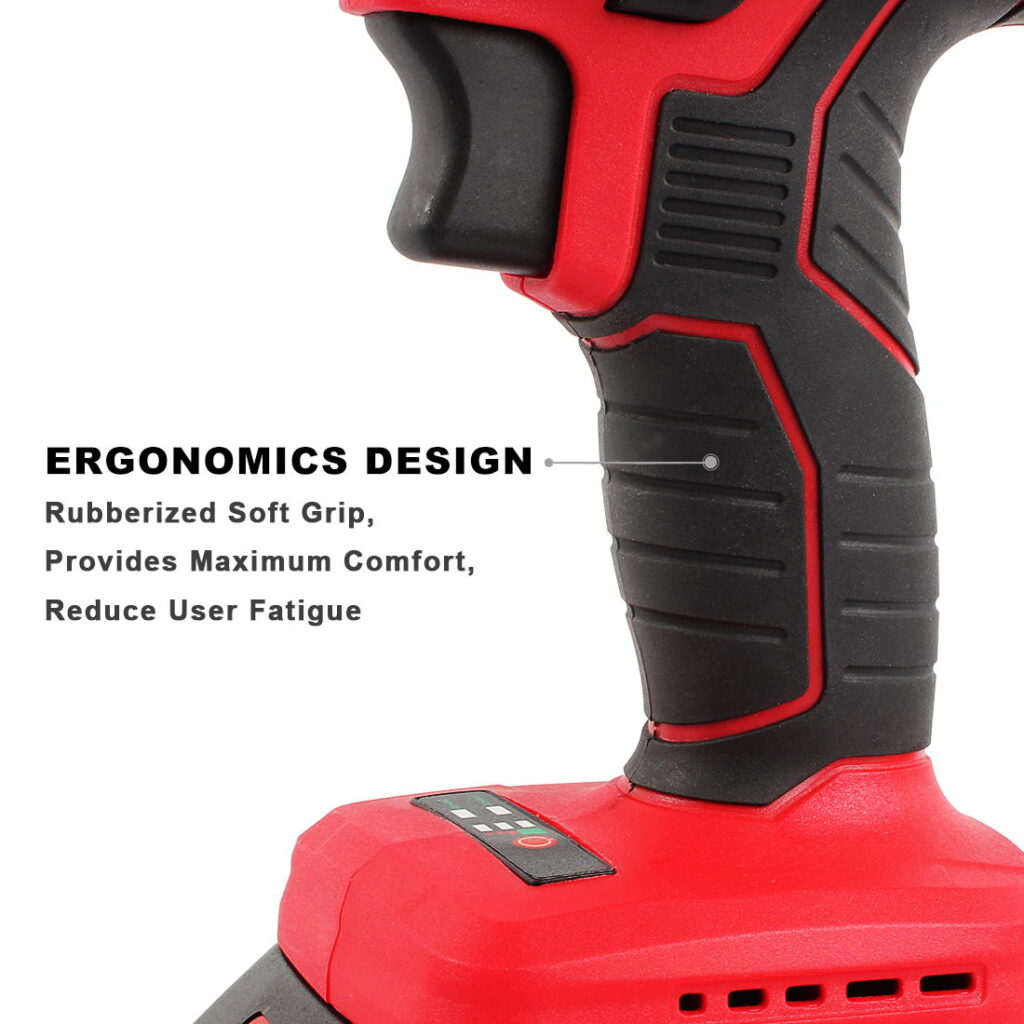
The Importance of Battery in Cordless Impact Wrenches
Our cordless impact wrenches are powered by top-of-the-line lithium-ion batteries, which have several advantages over older types like nickel-cadmium. These include higher energy densities, no memory effects (which means you can partially charge them without affecting future performance), and a slower loss of charge when not in use, making sure the tool is ready to go whenever you need it. Lithium-ion batteries are lighter, more efficient, and have no memory effect, which means you can charge them or top them off at any time without affecting their capacity or lifespan.
Advantages of Superior Battery Technology
Choosing the right battery technology affects not just the performance but also the comfort and design of the impact wrench. Lighter batteries make the tool weigh less, which decreases tiredness and makes it easier to move around. This design consideration is especially important for our ergonomic impact wrenches, which are meant to be used for a long time in various industrial applications. And higher voltage batteries give more power, which is needed for tougher jobs that require high torque. However, more power shouldn’t shorten the tool’s lifespan. That’s why our batteries are not just powerful but also built to make sure both the battery and the impact wrench last a long time.
Also, the efficiency of a battery affects how a tool performs under different temperatures and workload conditions. Our impact wrenches are designed to work efficiently across a wide range of environmental conditions, making sure they perform reliably whether indoors, in a heated workshop, or outside in colder climates. This reliability is key for professionals who need their tools to perform consistently, no matter where they are.
Impact of Battery Life on Long-Term Value
Investing in high-quality battery technology not only improves immediate performance but also adds to the long-term value of the tool. Batteries that can go through more charge cycles before they start to degrade not only make the impact wrench last longer but also reduce how often and how much you have to spend on replacements. This is a big consideration for businesses looking to make the most of their operational budgets.
Also, the reliability of a tool’s battery life is a key factor in maintaining consistent performance standards. Tools that can keep a high level of performance throughout their battery life give our clients the confidence that they can finish their tasks without interruption or loss of efficiency.
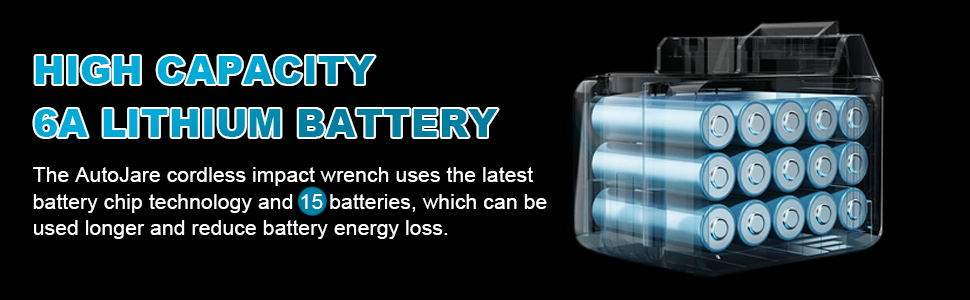
Conclusion
Choosing the right size and type of impact wrench doesn’t have to be hard. Focus on what your tasks need, think about the environment where you’ll be working, and don’t underestimate the importance of comfort and battery life for cordless models. At Autojare, we’re committed to providing our customers with high-quality, reliable tools that meet a wide range of needs. Whether you’re a brand retailer or a large supermarket buyer, we’re here to help you succeed with our products.