At Autojare, we understand that the tools you choose are crucial for your work, especially when they affect not just efficiency but also your working environment. Our experience in manufacturing cordless impact wrenches has taught us that while these tools are invaluable for their power and portability, their noise levels can be a concern for many professionals.
Why is Noise Management Important in Impact Wrenches?
Noise is an inherent part of using an impact wrench, typically ranging between 85 to 100 decibels (dB). This level of sound can pose risks to hearing over prolonged exposure. Thus, managing noise is crucial not only for user comfort but also for maintaining a safe workspace.
Continuing to operate without addressing noise can lead to significant health issues, including permanent hearing loss. This is especially pertinent in enclosed spaces where sound can resonate, amplifying the effects of noise exposure.
anaging the noise level of an impact wrench is not just about comfort; it’s about safety. For instance, prolonged exposure to noise levels above 85 dB can cause irreversible hearing damage.
Here is the information regarding noise levels and their impact on human health, this table outlines the decibel levels of noise and their corresponding impacts on human health as understood and regulated in the United States.
Noise Level (dB) | Description | Potential Impact on Human Health |
---|---|---|
Up to 60 | Normal conversation | Safe, no risk to hearing |
About 70 | Background noise | Possible fatigue or stress, no direct hearing damage |
85 and above | Starting level of potential risk | Risk of permanent hearing loss after prolonged exposure (8 hours) |
100 and above | Significantly dangerous | Short exposure (15 minutes) can damage hearing |
About 120 | Pain threshold | Immediate pain and potential immediate hearing loss |
140 and above | Extreme conditions (e.g., gunfire, explosions) | Almost immediate hearing damage |
How Can You Manage Noise Levels Effectively?
Managing noise levels effectively for impact wrenches involves a combination of strategies that focus on equipment design, personal safety measures, and workplace practices. Here’s a detailed approach:
- Select Low-Noise Models: Choose impact wrenches designed to minimize noise. Manufacturers may use advanced technology and materials that absorb and reduce sound output. Look for tools that are advertised with noise reduction features or have lower decibel ratings.
- Use Personal Protective Equipment (PPE): Always use appropriate ear protection when operating high-decibel tools like impact wrenches. Earplugs or earmuffs can significantly reduce the noise exposure to safer levels. Ensure that the ear protection used has an adequate Noise Reduction Rating (NRR) for the tool’s noise level.
- Regular Maintenance: Keep the impact wrench well-maintained. Regular maintenance can prevent noise increases caused by wear and tear. Ensure that all parts are properly lubricated and that any loose components are tightened, as loose parts can amplify noise.
- Isolate the Noise Source: If possible, isolate the impact wrench work area with sound barriers or operate within enclosed spaces designed to absorb sound. Using acoustic panels around the work area can help contain and reduce noise spread.
- Limit Exposure Time: Implement work schedules that limit the duration of exposure to noise from the impact wrench. Break up long tasks into shorter segments with breaks in between to reduce prolonged noise exposure.
- Train and Inform: Educate workers about the risks of noise exposure and the importance of using protective equipment and following recommended practices. Awareness can significantly improve compliance and reduce the risk of hearing damage.
- Use Alternative Tools When Feasible: For tasks that don’t require the high torque of an impact wrench, consider using quieter tools that can achieve the same results with less noise, such as torque wrenches or electric screwdrivers.
By combining these methods, you can effectively manage and reduce the noise levels associated with the use of impact wrenches, making the workplace safer and more comfortable for everyone involved.
What Innovations Has Autojare Introduced?
At Autojare, innovation is key. We have developed a series of brushless motor impact wrenches that not only reduce noise but also enhance efficiency and durability. These motors operate with less friction, a principal source of noise in traditional brushed motors.
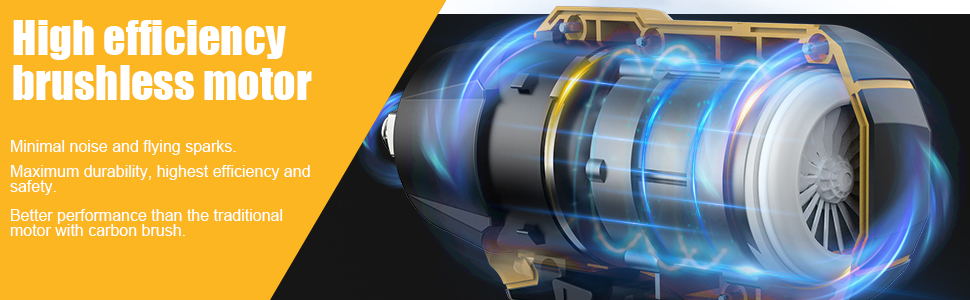
Additionally, we’ve incorporated vibration reduction technologies into our impact wrench designs. These innovations help dampen the physical feedback during operation, which not only reduces the sound but also lessens fatigue for the user.
Choosing Autojare means opting for a wrench that is built with both the user and environmental considerations in mind. Our products are a testament to our commitment to quality and sustainability. We ensure that every impact wrench we produce not only meets but exceeds industry standards for noise and safety.
Furthermore, our dedicated customer service team is always ready to support you in selecting the right tool for your needs, ensuring that you are fully informed about the noise management and safety features of our impact wrenches.
How Do We Ensure Product Availability and Quality?
Ensuring product availability and quality, particularly for tools like impact wrenches where noise levels are a significant concern, involves several key strategies focused on supply chain management, quality control, and customer service:
- Robust Supply Chain Management:
- Diversify Suppliers: Work with multiple suppliers to mitigate risks associated with reliance on a single source. This helps ensure a steady supply of raw materials and components.
- Inventory Management: Implement advanced inventory management systems that can predict demand more accurately and keep sufficient stock on hand to avoid shortages.
- Strong Relationships: Build strong relationships with suppliers and manufacturers to ensure priority during high-demand periods and better negotiate terms and prices.
- Strict Quality Control Processes:
- Design and Engineering: Invest in research and development to design impact wrenches that are both effective and optimized for lower noise levels. Utilize the latest technologies and materials that can absorb or dampen sound.
- Testing and Certification: Regularly test the products at various stages of production for both performance and noise levels. Certifications from recognized standards (like ISO) can also help in assuring quality.
- Continuous Improvement: Collect feedback from end-users and technicians to continuously improve product design and functionality, focusing on reducing noise and enhancing user safety and comfort.
- Customer-Centric Product Development:
- Feedback Mechanisms: Establish effective channels for customer feedback and genuinely incorporate this feedback into product development. This can help in understanding the needs and expectations related to noise levels and overall tool performance.
- Education and Training: Provide customers with information and training on the correct use of impact wrenches to optimize performance and minimize noise. This includes proper maintenance techniques and the use of personal protective equipment (PPE).
- Reliable Customer Service:
- Availability: Ensure that customer service is easily accessible and capable of providing prompt and informative responses.
- Warranty and After-sales Support: Offer robust warranty terms and efficient after-sales service to address any issues related to product quality or performance. This reassurance can build customer trust and loyalty.
- Innovation and Adaptation:
- Adopt New Technologies: Stay abreast of new technologies and industry trends that can help in making quieter and more efficient tools. For example, brushless motors in impact wrenches can reduce noise and enhance durability.
- Sustainability Practices: Incorporate sustainable practices in the manufacturing process, which can also affect product quality and brand perception positively.
Conclusion
By focusing on these areas, manufacturers of impact wrenches can ensure that their products are not only available when needed but also maintain high standards of quality and meet consumer expectations regarding noise reduction and performance.