An impact wrench also known as an impactor, impact gun, air wrench, air gun, rattle gun, torque gun, or windy gun, is a powerful tool designed to deliver high torque output with minimal exertion by the user, by storing energy in a rotating mass, then delivering it suddenly to the output shaft. It is commonly used for loosening lug nuts from cars and trucks, heavy equipment maintenance, product assembly, major construction projects, and any other instance where a high torque output is needed.
Types of Impact Wrenches
Impact wrenches come in various types, each suited to specific tasks and power sources:
- Pneumatic Impact Wrenches: Also known as air impact wrenches, these tools are powered by compressed air from an air compressor. operate by applying rotating energy or torque to the mass, then releasing it in a short burst, with the rotating energy or torque supplied by high-pressure air. For these wrenches to work, a steady supply of air is necessary, powered through an adapter and forced through a hole. This air interacts with a rotor, causing it to spin and build rotational energy. The rotor is connected to a hammer, the mass used to apply high force on a nut or bolt. They are known for their high power-to-weight ratio and are commonly used in automotive and heavy equipment maintenance.
- Electric Impact Wrenches: work similarly but are powered by a strong electric motor. They feature an impact function essential to their design, delivering strong rotational bursts of force inside the tool, transferred to the drill bit to screw in nuts and bolts. The impact function, activated upon encountering resistance, causes the hammer to slip from the engaging pin and rotate at a much faster speed in circular motion, transferring the stored energy in a short burst upon contact with the anvil again. If resistance is encountered again, the process repeats. These can be corded or cordless. Corded models require a power outlet, while cordless models run on rechargeable batteries, offering greater mobility.
- Hydraulic Impact Wrenches: Less common and used in specialized applications, hydraulic impact wrenches offer tremendous torque and are typically used in industrial and heavy construction settings.
How It Works
But how does this remarkable tool work? The core mechanism of an impact wrench involves a motor that powers a rotating mass. When the motor spins this mass, it stores energy, which is then suddenly transmitted to the output shaft in short, high-torque bursts or “impacts.” This mechanism allows the impact wrench to generate a significant amount of torque with very little effort from the operator. The action is somewhat similar to that of a hammer striking an object, hence the term “impact.” This repeated impact force is what helps to loosen or tighten fasteners quickly and efficiently.
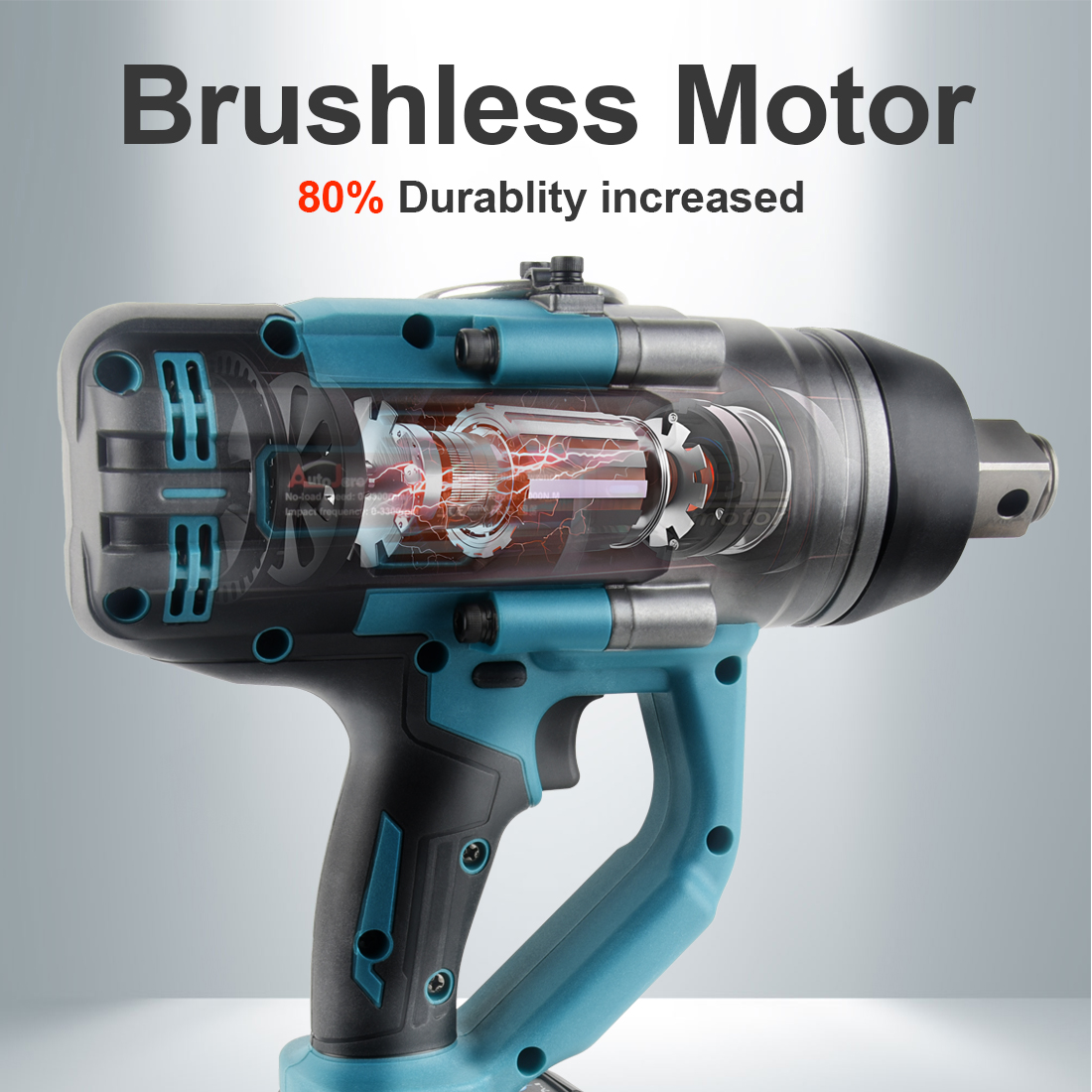
Why Is Torque Important in Impact Wrenches?
Torque, the measure of the force that can cause an object to rotate about an axis, is crucial in fastening and loosening nuts and bolts. essentially, is the turning force applied to an object such as a bolt or nut. In the context of impact wrenches, it determines the effectiveness of the wrench in tightening or loosening bolts. Higher torque values indicate a stronger capacity to deal with stubborn or over-torqued fasteners, making this specification a critical factor in the performance of an impact wrench.
Here’s a simplified table to illustrate how torque values can vary among impact wrenches and their implications:
Impact Wrench Model | Max Torque (Nm) | Ideal Usage Scenario |
---|---|---|
Model A | 100 Nm | Light automotive work, such as brake and wheel lug changes |
Model B | 500 Nm | General automotive repair, construction tasks |
Model C | 1000 Nm | Heavy-duty tasks, such as truck lug nut removal, industrial maintenance |
Model D | 1500 Nm | Industrial applications, large construction projects |
- Model A with 100 Nm of torque is perfect for smaller, more delicate operations where too much torque could cause damage.
- Model B offers a mid-range torque that suits a broad spectrum of automotive and construction tasks, balancing power and precision.
- Model C steps into the heavy-duty realm, ideal for tasks that require significant force, such as loosening rusted or over-torqued nuts.
- Model D, at the high end with 1500 Nm, is designed for the most demanding applications where maximum torque is necessary to accomplish the job.
This table showcases a range of torque outputs suitable for different tasks. For instance:
Understanding these specifications is crucial for selecting the right impact wrench for your needs. High torque is especially important in industrial and automotive settings, where fasteners need to be tightly secured or may have become difficult to remove over time. By choosing an impact wrench with the appropriate torque rating, users can ensure efficiency, safety, and the longevity of both the tool and the project components.
In summary, the torque value of an impact wrench directly affects its utility and effectiveness in various scenarios, making it a pivotal factor in the selection process for professionals and enthusiasts alike.
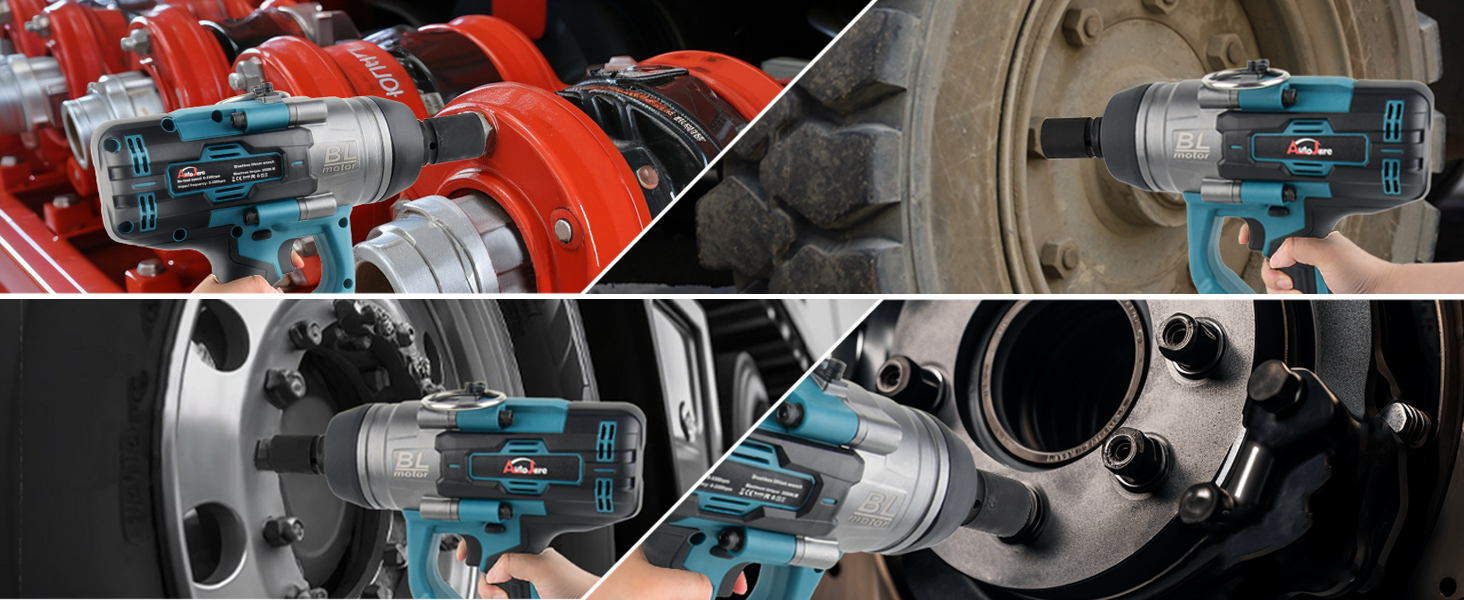
What Sets Impact Wrenches Apart?
Impact wrenches stand out from other tools due to their unique features and capabilities, especially when it comes to handling tough fastening and unfastening tasks. Here’s what sets them apart:
- High Torque with Minimal Effort: Impact wrenches are renowned for their ability to deliver high torque while requiring minimal effort from the user. This makes them ideal for loosening tight bolts and nuts that would otherwise be difficult or impossible to remove with manual tools.
- Bursts of Power: Unlike steady torque tools, impact wrenches work by delivering short, high-torque bursts. These bursts are generated through the internal hammering mechanism, which dramatically increases the tool’s effectiveness on stubborn fasteners without straining the user’s hand or wrist.
- Versatility in Power Sources: Impact wrenches can be powered by air (pneumatic), electricity (corded electric), or batteries (cordless electric), giving users a range of options depending on their needs and the work environment. Pneumatic models are typically used in professional settings for their high power and durability, while electric models offer convenience and portability for DIY projects.
- Precision and Control: Despite their powerful output, modern impact wrenches often come with adjustable settings that allow users to control the torque level. This feature is particularly useful for ensuring that fasteners are neither too loose nor overtightened, thereby reducing the risk of damage to the material or the fastener itself.
- Durability and Longevity: Designed to handle high torque applications, impact wrenches are built to withstand the rigors of heavy use. Pneumatic models, for instance, benefit from the cooling effects of compressed air, which helps prevent overheating and extends the tool’s lifespan.
- Efficiency in Tight Spaces: Some models of impact wrenches are designed with compact and ergonomic features, allowing them to fit into tight spaces where traditional wrenches or ratchets might not be able to go. This is especially beneficial in automotive work, where bolts can be located in hard-to-reach areas.
- Impact Mechanism Varieties: There are several types of impact mechanisms used in these wrenches, such as the pin clutch, twin hammer, and cam mechanism, each with its own advantages in terms of power delivery, durability, and suitability for different tasks .
In summary, the combination of high torque output, ease of use, versatility, and efficiency in challenging conditions makes impact wrenches a preferred tool for professionals and DIY enthusiasts alike. Their distinctive operation mode and variety of power sources and mechanisms provide a tailored solution for a wide range of fastening and loosening tasks.
How Do We Ensure Quality and Trust?
Adherence to Standards and Certifications: We strive to obtain and maintain certifications from recognized standards bodies, such as CE, to demonstrate our commitment to quality standards and continuous improvement. Our products meet industry-specific safety and quality standards, showcasing our dedication to excellence.
Quality Control and Assurance: Our robust quality control (QC) system inspects and tests products at various production stages, including incoming material inspection, in-process inspection, and final product testing. Quality assurance (QA) is also crucial in our process, managing procedures to prevent defects and ensure production quality through process audits, supplier quality management, and statistical process control. For instance, our Autojare cordless impact wrenches are designed for durability, using high-quality materials suited for heavy use.
Transparency with Stakeholders: We prioritize transparency in our manufacturing processes, quality control measures, and supply chain. This openness builds trust with customers, suppliers, and regulators. Offering detailed product information, including materials used and production methods, is part of our approach. Autojare provides competitive pricing without compromising quality or performance, ensuring great value for money for both professionals and DIY enthusiasts.
Investing in Technology and Equipment: Investing in the latest manufacturing technology and equipment enables us to enhance product quality and production efficiency. Autojare showcases this commitment by focusing on performance, including torque output, speed settings, and battery life, employing advanced battery technology like lithium-ion batteries for minimal downtime, and incorporating ergonomic designs and innovative features such as brushless motors and built-in LED lights. Advanced quality management software also plays a role in tracking quality metrics and identifying improvement areas.
Training and Employee Engagement: We regularly train our employees on quality standards, workplace safety, and emphasize the importance of their role in product quality. By fostering a culture where employees feel valued and empowered, we ensure they take ownership of their work’s quality.
Continuous Improvement: Our continuous improvement mindset, supported by methodologies like Lean Manufacturing and Six Sigma, helps us identify and eliminate waste and reduce variation in our production process. We value innovation and feedback from employees, customers, and suppliers to enhance our products and processes continuously.
Customer Feedback and After-Sales Support: Systematically collecting and analyzing customer feedback allows us to identify areas for product improvement. We pride ourselves on offering responsive customer service and solid warranties, further building trust with our customers by providing reliable after-sales support to handle inquiries and complaints promptly.
Supplier Quality Management: Working closely with suppliers ensures that materials and components meet our quality standards. This collaboration might involve supplier audits, setting quality requirements, and addressing quality issues together.
Regulatory Compliance: We ensure compliance with all relevant laws, regulations, and industry guidelines, including environmental regulations, labor laws, and product safety standards. Regular updates to our processes and products help us stay compliant with changing regulations.
Quality, delivery, service, and trust are the pillars of our relationship with customers. With over 100 professional specialists and strict quality control protocols, every impact wrench we produce reflects our commitment to excellence. Additionally, our rapid transportation times and close cooperation with the factory underscore our reliability in meeting customers’ urgent needs.
Conclusion
At Autojare, we’re not only just a manufacturer, we’re also a partner in your success. Our impact wrenches are crafted with precision, care, and a deep understanding of what our clients need. We invite you to experience the difference that dedication and quality can make to your business.
In a world where efficiency, reliability, and quality are non-negotiable, Autojare stands ready to meet and exceed those expectations. Let’s build a future where every nut and bolt is tightened with confidence, powered by Autojare’s cordless impact wrenches.